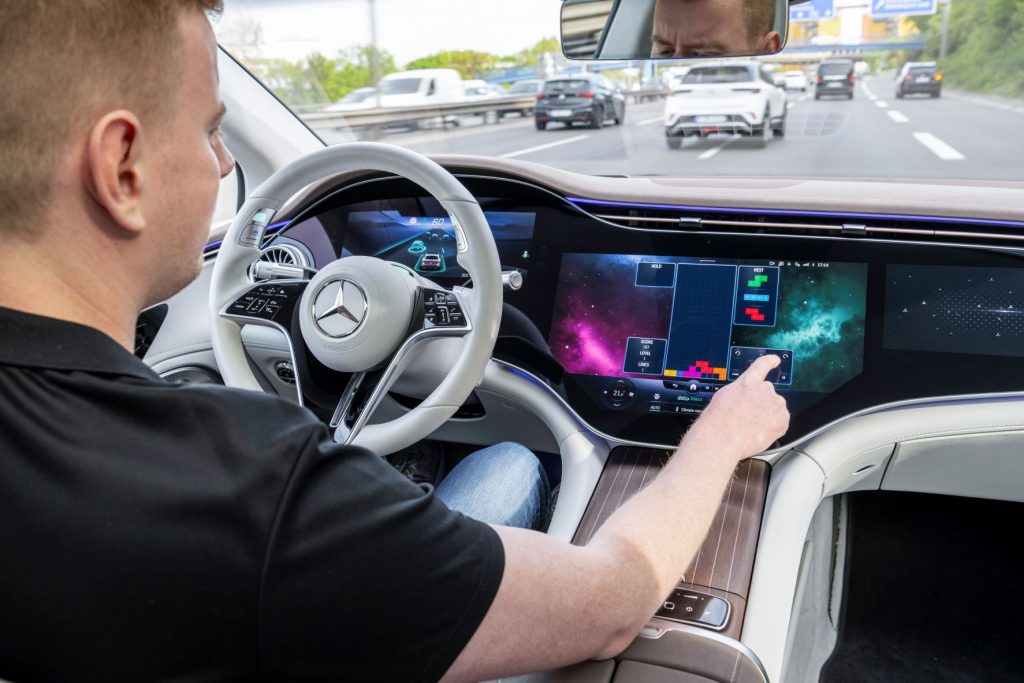
After announcing the system last year, the long-awaited market launch of the Mercedes-Benz Drive Pilot conditionally automated driving system can now be ordered as an optional extra for the S-Class (for €5000) and EQS (€7430). The system enables customers to hand the driving task over to the system under certain conditions in heavy traffic or congestion situations on suitable motorway sections in Germany up to a speed of 60 km/h (37 mph).
Drive Pilot is a big deal because the company says this makes it the first car manufacturer in the world with an internationally valid certification to offer such a system for conditional automated driving as an option for series production vehicles. It is classified as an SAE Level 3 system, with the automated driving function taking over certain driving tasks. However, a driver is still required and must be ready to always take control of the vehicle when prompted to intervene.
“Mercedes-Benz is the first manufacturer to put a Level 3 system with internationally valid certification into series production,” said Britta Seeger, Member of the Board of Management of Mercedes Benz Group AG, responsible for Marketing & Sales. “As a first step, we are offering this world-leading technology in Germany in the S-Class and the EQS.”
The automaker is also aiming for regulatory approval for the U.S. states of California and Nevada by the end of the year, provided the legal situation permits the system’s operation.
“Responsible handling of future technologies such as conditional automated driving is the key to acceptance among customers and in society,” added Seeger. “With Drive Pilot, we have developed an innovative technology that, thanks to redundancies with many sensors, enables safe operation and gives the valuable asset ‘time’ back to the customer.”
Legal framework and compliance
With the Road Traffic Act (or StVG) for SAE Level 3 systems in 2017, Germany says it became the first country to create the legal basis for the intended use of such automated driving systems. However, the technical approval methods did not come into force until the beginning of 2021. Since then, it could be implemented throughout Europe, an opportunity that Mercedes-Benz was quick to seize. It is the first auto company in the world to meet the legal requirements of the UN Regulation No. 157 (UN-R157) for Level 3 systems.
In detail, this results in requirements for the vehicle and duties for the driver. In conditional automated driving mode, the vehicle must master the driving task safely and comply with all traffic regulations. The driver still has duties on public roads to comply with other traffic regulations. And the driver must remain ready to take over and resume control when requested by Drive Pilot or due to other obvious circumstances.
Mercedes-Benz emphasizes that it is ensuring that the new technology is being put on the road in a legally compliant manner. Engineers, lawyers, compliance managers, data protection officers, and ethics experts have all worked together in the development process.
For safety-relevant functions such as pedestrian detection, Mercedes-Benz engineers deliberately do not use algorithms, for example through self-learning approaches. The focus is on what is known as “supervised learning,” meaning Mercedes-Benz defines and controls what the artificial intelligence (AI) is allowed to learn. Before the AI software is used on the roads, extensive validation testing is carried out to ensure that it works as desired in real traffic conditions.
In the case of pedestrian detection, AI helps the system to identify objects and situations on and next to the road quickly and safely. The detection process is designed to be non-discriminatory, meaning that the vehicle’s various sensors detect people correctly regardless of their clothing, body size, posture, or other characteristics.
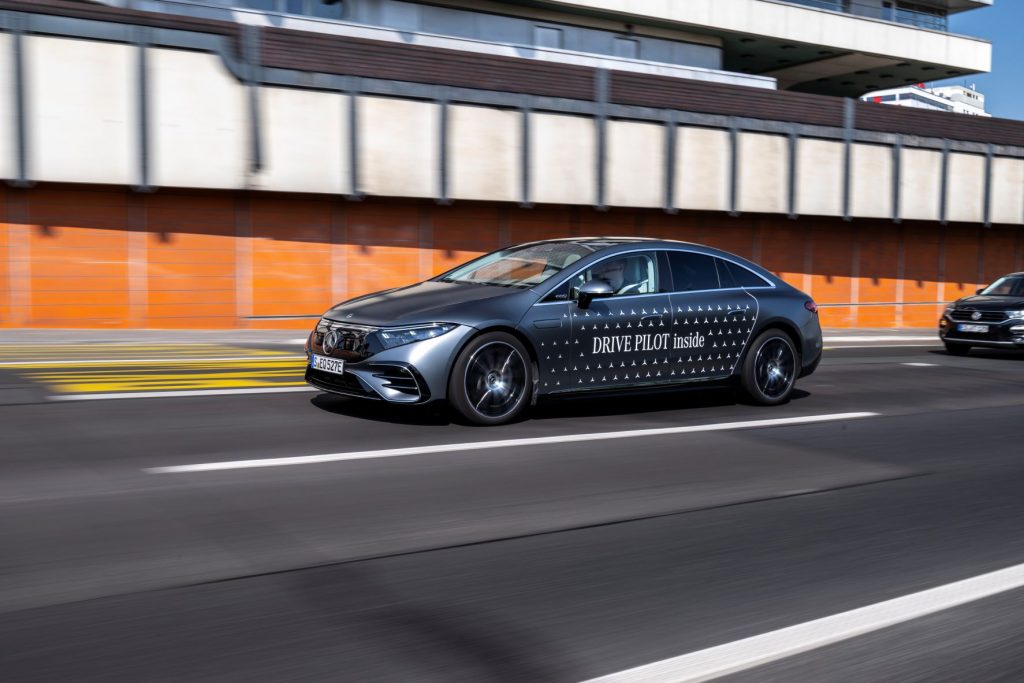
How it works
After activating, the Drive Pilot controls the vehicle’s speed and distance and guides it within its lane. The route profile, events, and traffic signs are all analyzed and taken into consideration. The system also reacts to unexpected traffic situations and handles them independently, for instance by means of evasive maneuvers within the lane or by using braking.
It builds on the tech behind the Mercedes-Benz Driving Assistance Package and includes additional sensors that the automaker considers indispensable for safe operation. The main sensor package includes radar, lidar, and camera sensors, but ultrasound and moisture sensors also provide valuable data.
Conditionally automated vehicle operation to SAE Level 3 requires a system design that must enable any malfunctions to be managed safely, providing a redundant architecture for the braking, steering, and power supplying systems. The need for redundancy also applies for sensor technologies covering functions for environmental awareness and driving dynamics calculation and for battery, steering motor, wheel speed sensors, and the various algorithms used by the system.
In the event of a malfunction, the redundant design allows the Drive Pilot to perform a safe handover to the driver. If the driver does not comply with the takeover request within 10 s, the system initiates an emergency stop that is safe both for the vehicle and following traffic as calculated by the Intelligent Drive Controller.
The company says that a Drive Pilot-equipped Mercedes uses a high-precision positioning system that is much more powerful than conventional GPS. In addition to the anonymized data collected by lidar, camera, radar, and ultrasound sensors, a digital HD map provides a 3-D image of the road and the surroundings with information on road geometry, route characteristics, traffic signs, and “special traffic events” like accidents or construction.
The high-precision map features centimeter accuracy, and map data are stored in back-end data centers and continuously updated. Each vehicle also stores an image of this map information on board, constantly compares it with the backend data and updates the local dataset as required.
All of this enables stable and accurate positioning through a representation of the surroundings that is independent of factors such as shadows or dirty sensors.
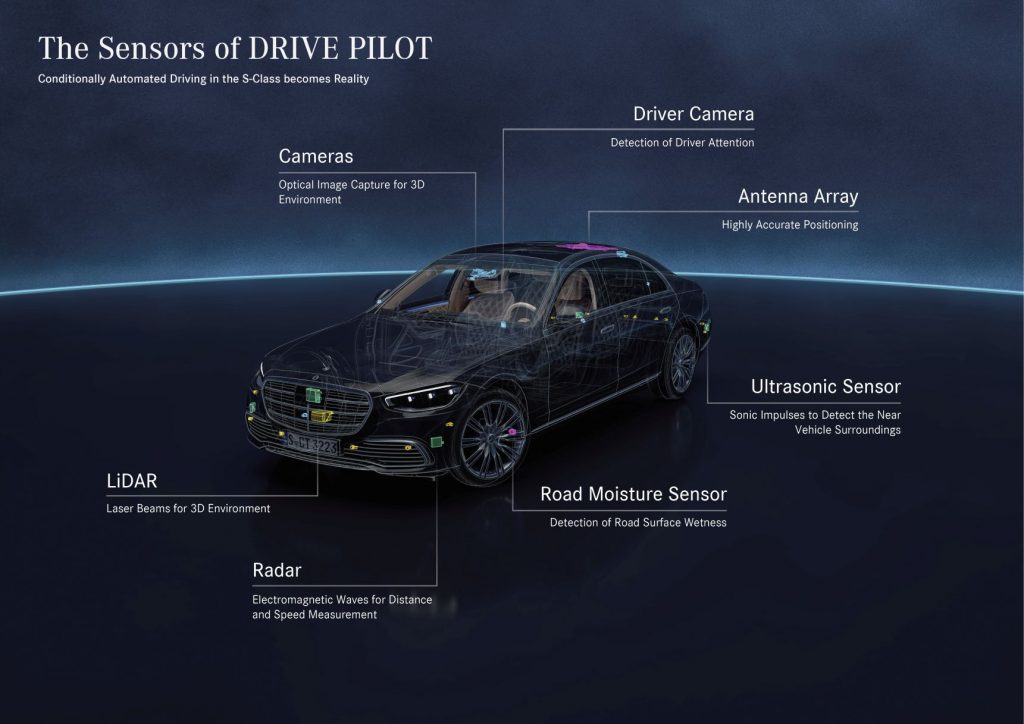
Help from suppliers
Veoneer, Inc. supplies some of the key building blocks of the Drive Pilot system.
The company announced in September that it is providing its fourth-generation stereo vision camera system comprised of fully integrated hardware and perception software. It’s CNN (Convolutional Neural Network) technology enables accurate classification and positioning of objects in front of the vehicle.
Functions enabled by the stereo camera are lane detection, free space, small obstacle detection, and 3D objects classification—of vehicles, motorbikes, pedestrians, lanes, landmarks, signals, and posts—under a variety of weather conditions. The stereo camera also contributes to the detection of emergency vehicles and construction warning trailers to support Level 3 driving.
The supplier’s 77-GHz radar system, generation 1.2 that includes corner radars, has been adapted to support the Level 3 solution. The latest 77-GHz radars use super-pulse modulation techniques for enhanced perception, operating at a distance up to 150 m (490 ft) with high range resolution and angular accuracy. Compared to their predecessor, they have 50% more range in the rear corners to detect motorcycles and over 100% more range in the front corners.
The radars are key components contributing to the vehicle’s spatial awareness, which is increasingly important for the Level 3 use cases. Software algorithms help to provides better angular resolution, allowing the Drive Pilot system to discern pedestrians and vehicles.
“Our world-class products are an integral part of the Drive Pilot system, but more importantly, I am even more proud of our way of working closely integrated with our customer in an agile manner, ensuring the end-consumers get superior features that improve driver convenience and safety,” said Jan Carlson, Chairman, President and CEO of Veoneer.
At CES 2022 in January, Here Technologies announced that it was among the world’s first companies to provide an HD (high definition) map for commercial production vehicles with Level 3 automated driving capabilities for the Drive Pilot system. In combination with the input from vehicle sensors, Here’s cloud-based HD Live Map data are used to maneuver the Drive Pilot-equipped vehicles on public roads.
The supplier says that its map enables an automated vehicle to effectively “see around corners” by delivering precise information about the road network and rules of the road—including detailed lane-level data, road and intersection geometry, signage, and driving restrictions.
Here says it has built one of the world’s largest enterprise-grade location data platforms, capturing and indexing the world’s road networks and urban environments to create highly accurate, 2- and 3-D maps from thousands of data sources. The company is developing its platform to offer software developers and the auto industry a one-stop shop for location data, services, and software.
In May, in conjunction with the release of its 2021 fiscal year financials, TÜV Rheinland said that it assisted with the homologation of the world-first Level 3 Drive Pilot system for the S-Class and EQS. An interdisciplinary team of experts supported the effort in accordance with UN-R157 requirements over a period of about two years, the system receiving approval from the KBA (Kraftfahrt-Bundesamt), the German Federal Motor Transport Authority.
“Even though advanced simulation technologies make it possible to reduce the real testing effort, simulation alone is still not enough,” said Rico Barth, Head of the Connected and Automated Mobility global business segment at TÜV Rheinland. “In development and for approval, more complex scenarios need to be tested on real test tracks.”
For the project, TÜV Rheinland engineers provided support for dynamic driving tests on Mercedes test tracks and public roads.