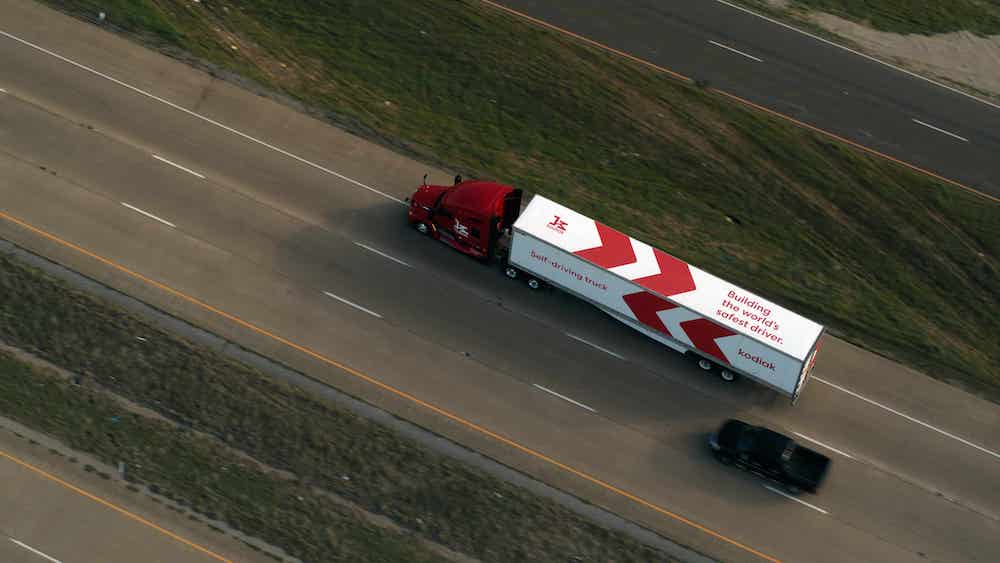
Autonomous vehicle startup Kodiak Robotics may be the first company to publicly demonstrate the fallback system its self-driving vehicles use to guide themselves out of traffic in the event of a critical system failure, the firm announced May 12.
Although critical failures such as blown tires and engine problems are uncommon in motor vehicles, they can prove very dangerous if not handled properly.
“To launch an autonomous vehicle without a human driver, you must ensure the vehicle will protect motorists in the case of a truck or autonomous system failure,” Don Burnette, founder and CEO of Kodiak, said in a statement. “Implementing a fallback system is a fundamental necessity to achieving that level of safety. We are the first autonomous trucking company to demonstrate this capability on public roads.”
Kodiak explained that 10 times each second, its self-driving system, the Kodiak Driver, analyzes the performance of more than 1,000 safety-critical processes and components in both the self-driving computer stack and the vehicle platform. These include autonomous vehicle system components such as sensors and software processes, as well as truck-related components such as the engine, oil levels and tire pressure.
“We have integrated fallback technology into the Kodiak Driver’s architecture from the beginning—it would be incredibly hard to add this capability as an afterthought,” Burnette said in a statement. “It’s essential that the self-driving technology powering an 80,000-pound semi-truck is capable of reacting swiftly and safely, no matter what happens.”
Should any of one of Kodiak’s self-driving truck’s critical components fall outside acceptable performance parameters, the Kodiak Driver will automatically assume a minimal risk condition, safely pulling the vehicle over to the side of the road.
“We have architected the Kodiak Driver from the start to always have a backup plan,” Felix Duvallet, technical lead and manager at Kodiak, said in a blog post. “This backup plan, known as a fallback, must go beyond low-level strategies such as blindly applying the brakes or randomly pulling over: fallbacks must be carefully planned maneuvers designed to bring a truck to a controlled stop in a safe location. Think of it as a ‘rainy day’ contingency made ahead of time: in the extremely rare occurrence that a major fault does occur, the Kodiak Driver will detect it, and spring immediately into action based on its fallback plan. Fallbacks should almost never be used, but they are critical to ensuring safety.”
Burnette noted that Kodiak’s ability to perform safe fallbacks “depends on our own custom-designed safety computer, the Actuation Control Engine, or ACE. One of the many crucial functions the Kodiak ACE is responsible for is ensuring that our autonomous system can guide the truck to a safe stop when necessary.”
Just as the human brainstem is able to react quickly without waiting for input from the rest of the brain, Kodiak’s ACE safety computer executes a fallback without input from the Kodiak Driver’s main computer. Kodiak’s fourth generation of trucks includes two ACE units for redundancy and additional safety. Should the ACEs lose connection with the Kodiak Driver’s main computer for any reason, from a communications failure to a loose cable, the system will automatically execute a fallback. Kodiak is currently working to certify the safety computer to the highest automotive-grade standard.
Duvallet noted it can be a challenge to test and validate fallback functionality, since it will very rarely be used on the road. “This is one of the areas where Kodiak’s investments in simulation and structured track testing have paid off,” he said in a blog post. “We leverage large-scale simulation capabilities to constantly simulate fallbacks. Similarly, we have designed complex scenarios for testing at track. We perform fault injection to trigger a fallback maneuver in all sorts of conditions: near objects, on curves, and of course in nominal driving conditions. Together, these give us confidence in the Kodiak Driver’s ability to safely perform fallbacks before going on the highway.”
Founded in 2018, Kodiak has been delivering freight daily on the 240-mile lane from Dallas to Houston since mid-2019, and on the 280-mile lane between Dallas and San Antonio since mid-2021. In February, it launched commercial operations between Dallas and Oklahoma City, and in April, it started the first commercial autonomous trucking lane to the East Coast, a route connecting Dallas-Fort Worth and Atlanta. Given all this driving, a safe, reliable failsafe technology is key.