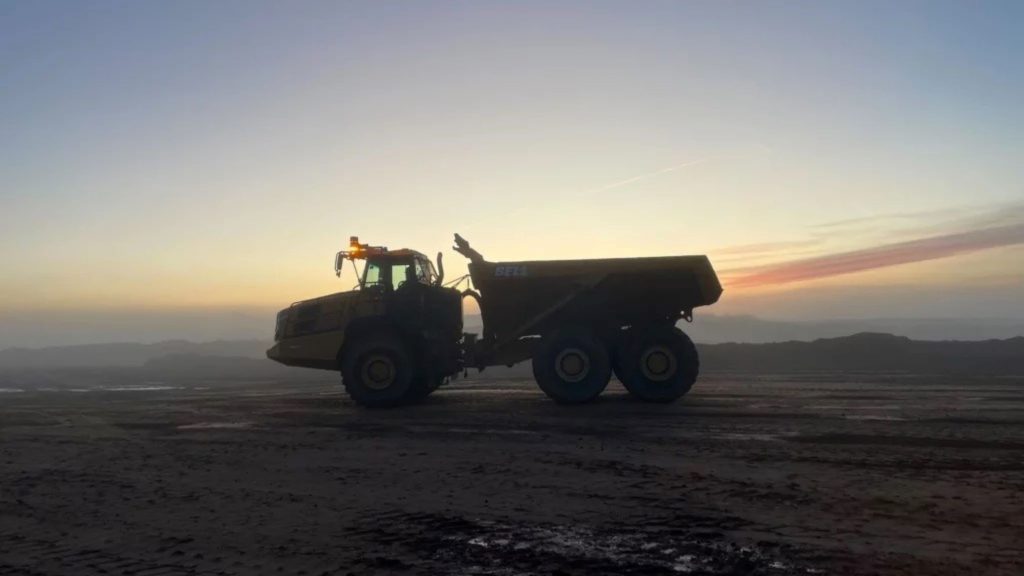
Mining industry strategic planning consultancy Whittle Consulting and the Silicon Valley-based autonomous haulage system (AHS) developer Pronto have released results of a study demonstrating that when mining haul trucks are automated, bigger is no longer always better. For “Autonomous Swarm Haulage: The Economics of Autonomous Haulage with Small Trucks,” Whittle Consulting modeled the net present value (NPV) of mining a representative copper ore body through four different scenarios, considering all facets of the mining value chain over an 18-year life-of-mine (LOM) horizon.
Key findings include that the modeled mine, operating with a fleet of autonomous 40-ton haul trucks, would realize a 31% greater NPV than if the mine were operated with a fleet of manually driven 100-ton off-road haul trucks. The study showed that autonomy significantly improved effective utilization by reducing truck downtime, standby, and operating delays to 5% of availability versus 20% for manual vehicles.
One theorized flaw in the small-truck logic was the prospect of traffic congestion caused by the increase in the number of trucks operating in the mine, potentially overcoming the efficiency gains of small trucks and automation. In the study’s simulations, such traffic congestion did not materialize.
“The industry has long debated whether mining economics shift to favor smaller trucks when autonomous,” said Gerald Whittle, CEO, of Whittle Consulting. “We’re excited to publish the first rigorous analysis that demonstrates that for most mines, the answer is yes.”
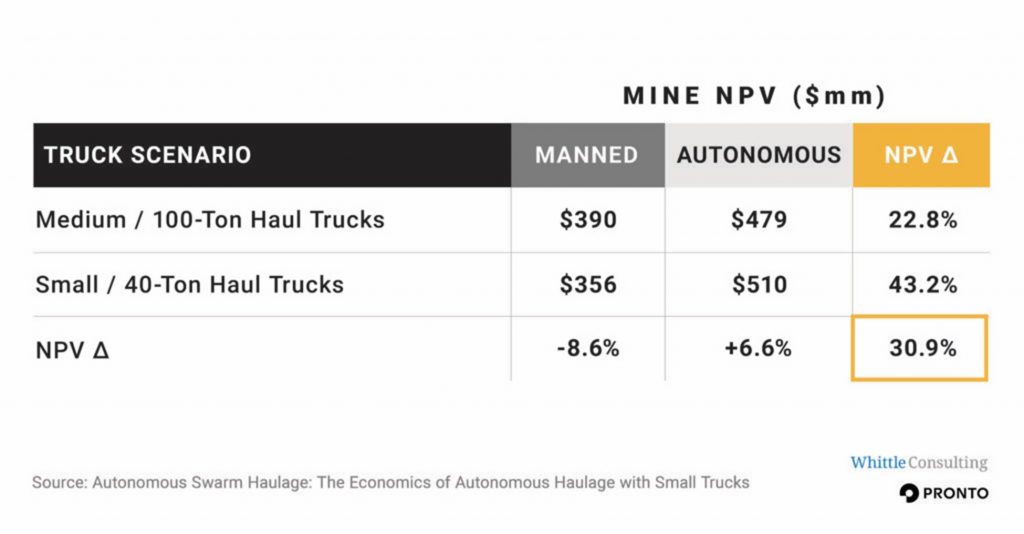
The study also concluded that converting an existing fleet of haul trucks to autonomous operations increased NPV irrespective of truck size. Both conclusions are consistent with industry experience and past studies including Whittle Consulting’s 2018 autonomous haulage report.
“This study is exciting because it clearly articulates one of the many ways in which autonomy is revolutionizing the global economy today,” commented Anthony Levandowski, CEO of Pronto. “The results also illustrate why our strategy has been centered around making automation accessible to the majority of mines and quarries around the world that aren’t running the Ultra Class trucks that the legacy AHS providers have been focused on.”
Pronto had previously demonstrated the commercial benefits of an AHS capable of scaling down to the smallest trucks and operations. The Pronto-Whittle study substantiates that by identifying the specifics of why small trucks are favored when autonomous including lower maintenance costs, better fuel efficiency, faster haul speeds, narrower benches/steeper pit walls are possible, and better overall fleet utilization.
In January, Pronto said its AHS for surface mines and quarries can operate with fewer than ten trucks in the 30- to 150-ton capacity range, bringing the benefits of autonomy to smaller operations at a fraction of the cost.
Its turnkey software and hardware system enables protection with situational awareness through GNSS and wireless communications, with a camera and GPS-based hardware stack that is lighter, faster, and more affordable to deploy. Its software-based solution eliminates “brittle” sensing hardware like lidar and radar.
The company’s software learns a haul route from a mining operator manually driving a vehicle on the desired route just one time. Operators then dispatch trucks to saved routes from their smartphones via a simple-to-use mobile app, eliminating the need for a control room. The system is built for production rollout in weeks, with no upfront commitments or years-long feasibility studies needed.
With low-cost hardware, increased utilization, and optimized operation, all this adds to a fast return on investment for AHS deployments.