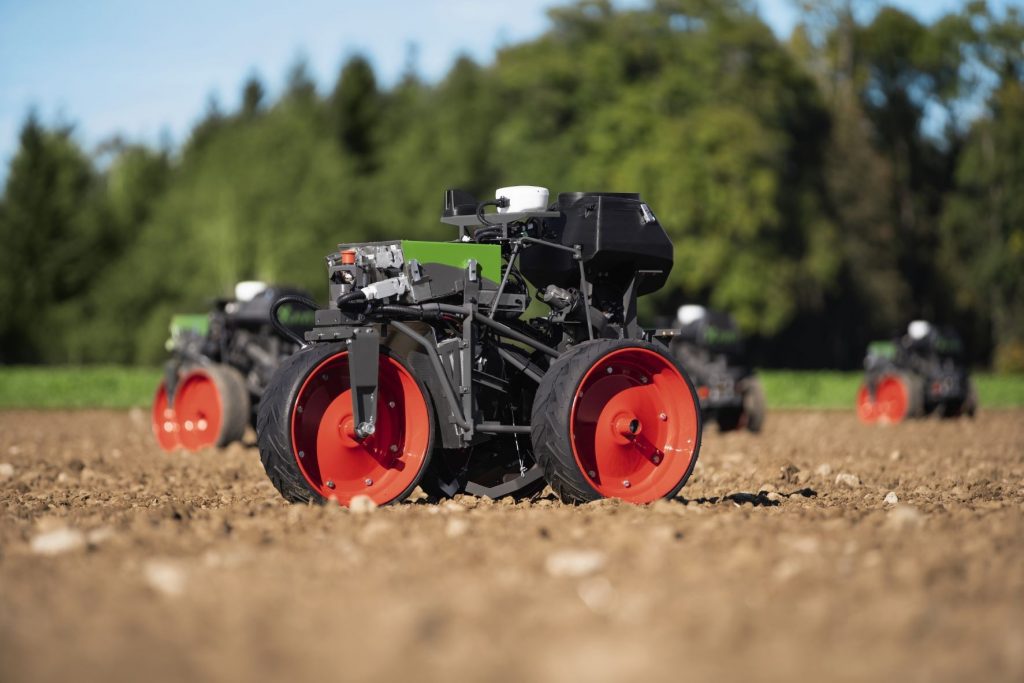
Apex.AI announced today that ag-machinery giant AGCO is adding new capabilities to its Fendt Xaver autonomous farming robot concept using the former’s Apex.OS software development kit (SDK). The move has enabled AGCO’s engineering team to quickly integrate several autonomous driving components into the ag robot including lidar object detection, collision checking, and planning using the framework and developer tools that come with Apex.OS.
The technical partnership expands an existing relationship between the two companies. In December 2021, AGCO announced a strategic investment in Apex.AI, headquartered in Palo Alto, CA.
“The technology has helped AGCO shorten R&D timelines of our smart agricultural solutions and for the future of highly automated robots,” said Christian Kelber, Director, Engineering, AGCO. “Coming from the automotive industry, Apex.AI enables us to implement safety-critical applications from autonomous driving that can be deployed across our range of solutions globally.”
Founded in 1990 and headquartered in Duluth, GA, AGCO is a global leader in agricultural machinery and precision ag technology with a portfolio that includes core brands like Fendt, Challenger, Massey Ferguson, and Valtra. Its full line of equipment and services helps farmers sustainably feed the world with help from Fuse smart farming solutions.
The Xavier autonomous robot concept, developed by Fendt as part of a research project, enables targeted seeding using swarms of sizes determined by application. The concept uses 90% less energy than conventional machines because of its lightweight and all-electric zero-emission design.
The system plants seeds on farms 24 h a day with centimeter precision, with AGCO leveraging Apex.OS to develop a software stack for extending Xaver’s real-time autonomous functions. A cloud-connected fleet of Xaver robots is controlled through an app and provides real-time data from each unit including its location, status, and diagnostics.
“We are leveraging our success in the automotive and autonomous driving industry and applying it to areas that have similar functional safety needs such as agricultural, industrial, mining, and construction,” said Jan Becker, Co-founder and CEO, Apex.AI. “Apex.OS allows the software architecture to be modular, scalable, and safe, enabling customers to transition their R&D projects to commercial-ready products in record time.”
Developing machines like Xaver requires a modern software architecture and agile development processes. Its software stack performs real-time autonomous functions using hardware such as camera, radar, and lidar sensors as well as GNSS (Global Navigation Satellite System) technology.
According to Apex.AI, there is an increasing trend of autonomy in agriculture, and designing and deploying a safe autonomous system is a complex and time-consuming task. The company is helping its agriculture, automotive, and industrial customers reduce the complexity of software-defined vehicles and machines with Apex.OS.
In 2021, Apex.OS achieved ISO 26262 ASIL-D, the highest level of automotive software safety possible. The company says that it is the first time that a significant, complex, modern C++ product was able to meet the stringent requirements of determinism and real-time behavior needed for a safety-critical use case.
Agricultural, industrial, mining, and construction machines have similar functional and safety needs as automobiles, easing the transition to Apex.OS for developing complex safety-critical functionality that can be deployed in areas with human interaction. It is also helping customers build systems to reach similar safety goals—such as ISO 25119 and ISO 18497—required in their highly automated industrial and agriculture machines.
According to a recent industry report from Deloitte cited by Apex.AI, the cost of integration, testing, verifying and validating functions to meet [quality and safety] requirements can easily amount to 40% or more of overall development budgets.
Apex.AI says it is helping its automotive and industrial customers in this regard by addressing the exploding complexity of software-defined vehicles and machines. Apex.OS allows the software architecture to be modular, scalable, and compliant to the requirements of safety-critical deployments. In addition, it provides the functional and performance testing and validation methodologies and tools developed for modern C++ based systems so its customers can reach production quality in their R&D projects even before pre-production engineering begins.
“Apex.AI’s modular stack enables us to transition from a prototype stack to a production stack in a seamless way,” said Tobias Nothdurft, Team Lead Research & Advanced Engineering at AGCO GmbH. “The stack we develop can run on a wide range of hardware platforms, allowing us to integrate smart technology developed here across the wide array of AGCO product lines.”
Designing and proving a safe autonomous system such as Xaver can be a complex and time-consuming task. For example, deterministic behavior needs to be designed into and validated for every component of the software stack.
“A control system with low-latency interactions between trajectory updates and collision checking can lead to a lot of engineering time spent on synchronization of messages between multiple publishers and subscribers in a deterministic way,” said Benjamin Fernandez, Project Engineer, Robotics, AGCO. “Apex.AI’s deep resources, including examples and articles, helped to select the right time policies and save valuable design time.”
Helping ease the integration of autonomous driving components is Apex.OS’ compatibility with common open-source tools.
“Virtually no engineering time was spent on training since Apex.OS is compatible with familiar open-source tools such as the Gazebo simulator,” said Michael Aeberhard, Application Engineering Lead, Apex.AI.
“Our software is safety certified, real-time, hardware agnostic, and simplifies the use of complex middleware interfaces,” added Frederik Beaujean, Application Engineering, Apex.AI.