A fully autonomous, battery-electric prototype by Volvo Construction Equipment, the LX03is the first real-world example of a self-learning concept wheel loader with the brains to make decisions, perform tasks, and interact with humans. It is also the first time ever a LEGO Technic model has been turned into a real machine. While not commercially available, engineers expect that valuable insights from the LX03 will feed into applications for today and tomorrow.
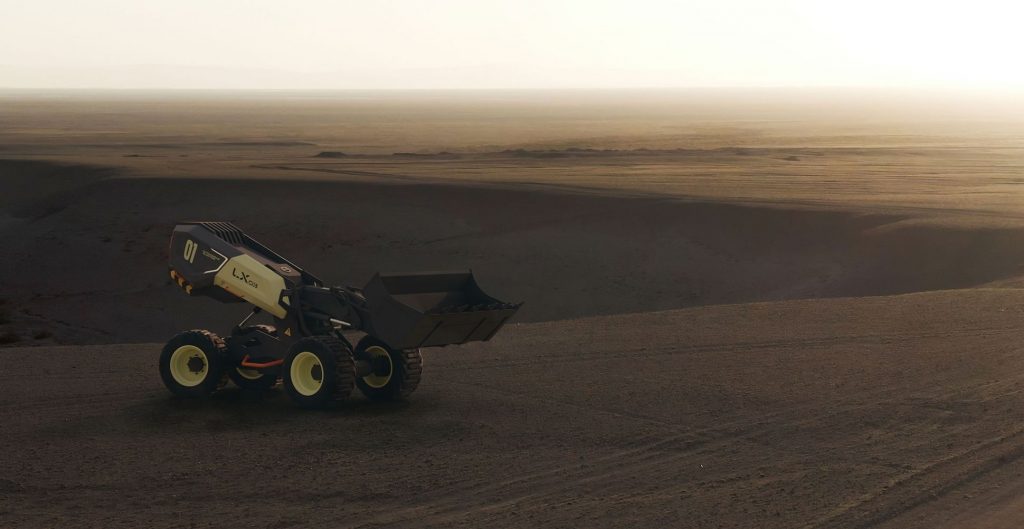
The prototype LX03 os a 5-ton wheel loader that has been developed as a modular concept, with the capability of being made larger or smaller with just one or two changes to the manufacturing process. It also shares its driveline with the L25 Electric, making it a zero emission, low-noise machine with a runtime of up to eight hours depending on its application.
It is designed to be a smart and safe worker, equipped with a brain that has the capacity to adapt to different scenarios, make decisions in real-time and most importantly collaborate with humans. It can be programmed by customers to complete heavy, repetitive or dangerous tasks, reducing the need for a human on site.
It represents Volvo CE’s drive to exploit machine intelligence and its determination to decarbonize the construction industry.
The LEGO Group’s Head of Product for LEGO Technic, Niels Henrik Horsted says: “Our two companies have enjoyed an extremely successful partnership over the years in which we have collaborated on several LEGO Technic models. But this is the first time we are making a real machine based on a model and not the other way around – and that is what makes this a truly unique project.”
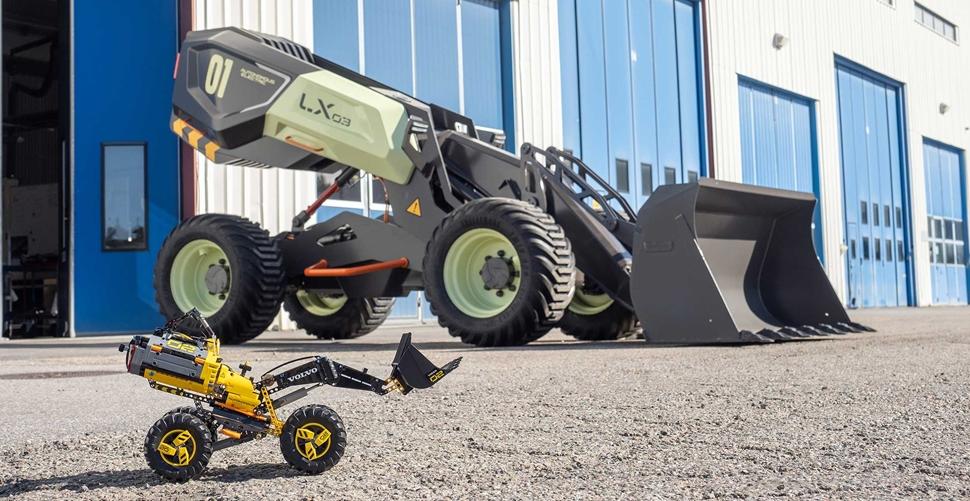
The LX03’s striking scissor frame is a unique feature that allows the machine greater freedom of movement and increased efficiency. It also offers a unique bucket sequence whereby the bucket can be filled by simply lowering the rear part, or counterweight, of the machine, requiring no work from the loading unit at the front and providing improved stability during the loading process.
When it comes to emptying the load, the counterweight, which also doubles as the battery pack, can then by lifted off the ground allowing the bucket to reach much further over the load receiver than a conventional machine. This motion pattern improves energy efficiency, because it not only allows the machine to use its own weight to create greater lifting power, but also allows for larger bucket fills thereby reducing the loading cycle.
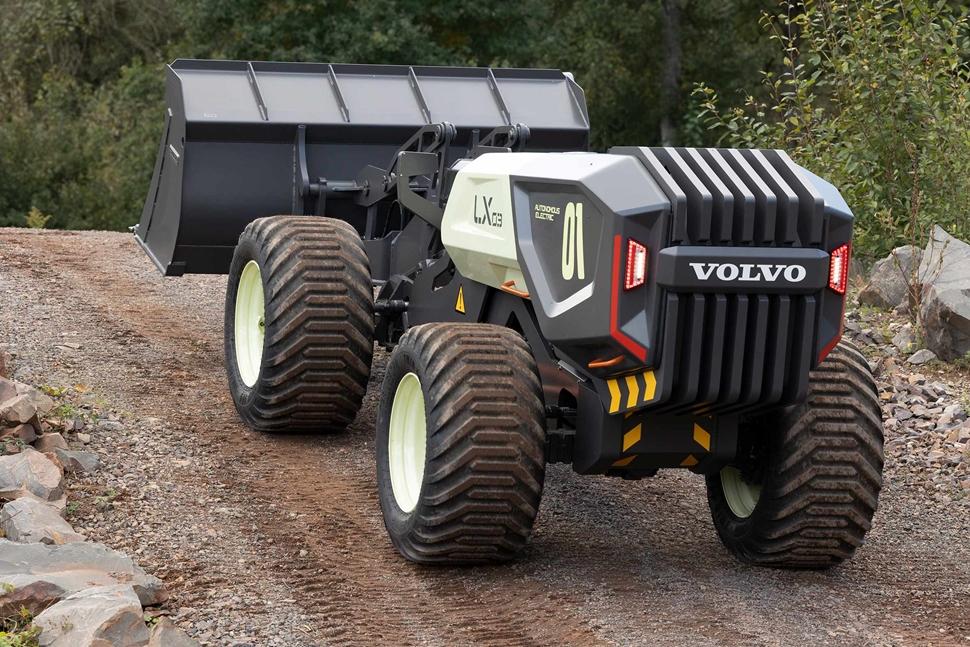