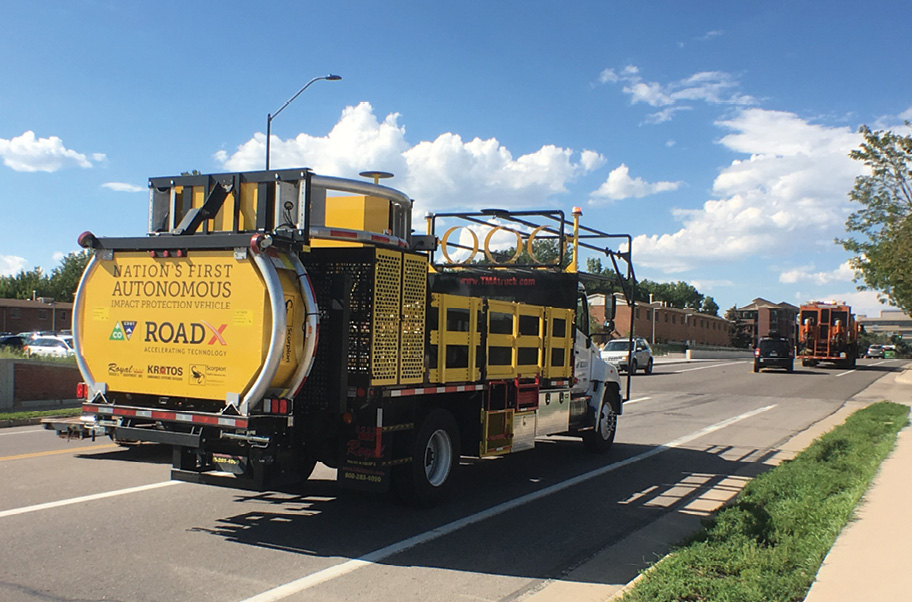
In 2017, 799 people died from roadside work zone accidents across the United States. Military developer Kratos Defense & Security Solutions, joined by Royal Truck & Equipment, has fielded an Autonomous Truck Mounted Attenuator to curb the carnage.
In Greek mythology, the god Kratos emblemizes strength, so much so that he supervises the binding of a Titan, Prometheus, for sharing fire with we mere mortals.
In the general population, Kratos’ current fame is as the star of the popular “God of War” video games.
But in the defense world, San Diego-based Kratos Defense & Security Solutions is flying high—in both senses of the phrase. Successive days this June saw the firm win air force and navy contracts for target drones. And with growth across divisions from unmanned systems to microwave electronics to turbine technologies, the stock market launched a 39% gain in Kratos stock over the month of May.
Kratos also has scored by transferring technology to an under-the-radar domestic war zone—the world of roadside construction and repair. As a harrowing car-crash video from Kratos civilian partner Royal Truck & Equipment reveals, a stunning 799 road crew and civilian drivers died in work zone accidents across the U.S. during 2017.
MIGRATING TECHNOLOGY
“In the military, we’re teaching minimum exposure to risk,” noted Maynard Factor, director of business development for Kratos’ Unmanned Systems Division. “The concept here was to eliminate dangerous job situations through driverless technologies.” Factor works out of Kratos’ Fort Walton Beach, Florida, facility, and has been with the company since 2011.
Kratos’ highway safety solution is the ATMA, or Autonomous Truck Mounted Attenuator. In this configuration, a human-driven “Leader Vehicle” is followed by an unmanned “Follower Vehicle”—the ATMA. The two vehicles utilize Kratos’ automation components to enable unmanned operation, and the system can be driven manually if needed. Both trucks carry an onboard computer, a V2V communications system (encrypted, frequency hopping, non-line of sight), and an operator control unit and user interface. The Follower vehicle adds actuators for steering, braking and acceleration control, as well as sensors for dealing with obstacles, e-Stop redundancy and a video camera. GPS data—“eCrumbs”—is transmitted back to the Follower vehicle, which synchs itself to the Leader’s position, path and speed.
The intent is for the ATMA to protect with precision. If an errant driver veers into a work-crew zone or runs up on, say, slow-moving road-striping equipment, the rearmost, now-unmanned, truck takes the brunt of the impact. A highway worker no longer has to risk piloting a moving crash barrier. Lifelong injury, painful rehabilitation and even death can be mitigated or avoided—as can legal and medical costs that can reach seven figures an incident.
Initially, the ATMA met a Department of Defense objective: to reduce what Kratos literature describes as “the number of warfighters needed to support dangerous Forward Operating Base [FOB] resupply efforts.” Then, in 2014, Factor recalled “demonstrating one of my autonomous military vehicles when somebody from a department of transportation stopped by and said, ‘I didn’t realize you could retrofit a vehicle for highway work.’ ”
Factor sees the battlefield-to-roadside shift as evolutionary. “We really changed very little; we took off the rocket launchers,” he joked. “We were able to leverage the technology. The hardware control systems leveraged very well.”
But if Kratos was on top of the ATMA system, it still needed a commercial partner. And so, Kratos went to Royal, which Factor saw as “a subject matter expert dedicated to safety in the highway maintenance arena. …They are the largest manufacturer of TMA trucks in the U.S., and have a ton of technology on the vehicles already”: radar, cone deployment and retrieval equipment, among other features. “They were on board right away. Within a week, they sent me a truck for testing.”
Fred Bergstresser, Royal’s government account manager, outlined the ATMA’s commercial advantages.
“The primary thing is, it takes the driver out of the crash vehicle and the attenuator saves the life of the motorist. Hitting a truck full of gravel or stone would kill the motorist. …[Now]…“they could basically get out of their car or truck and not be injured.”
Bergstresser offered examples. “Line-painting at 7 miles an hour, other operations up to 15, they’re all slow-moving on a fast-moving highway. What we’ve done, with Kratos, is make the paint truck the lead truck and the attenuator the follower truck, the shadow vehicle, the impact protection vehicle.”
Until recently the sole suitable crash-absorber technology was the Scorpion, a honeycombed, aluminum impact-resister made by TrafFix Devices, a San Clemente, California, company. It’s now been joined by the Blade, from Verdegro of Holland, whose metal-cutting-into-metal premise stretches the crash impact over a couple of seconds.
“We can use either one,” Factor said. “Both passed the latest crash test.”
Prices vary per configuration, but, overall, a road-ready ATMA system can run $350,000, including tech, truck, attenuator and on-site training.
ROLLING (OUT) PROTECTION
Royal is based in Coopersburg, Pennsylvania, and a mid-decade product demonstration received media coverage. Interestingly, though, the first contract came from the UK division of Colas, which bills itself as “the world leader in road construction.” In 2017, that system—known in Europe as the AIPV (Autonomous Impact Protection Vehicle)—began rolling on the M-3 Motorway south of London. In this case, Royal retrofitted existing trucks.
The Colorado Department of Transportation followed suit. “They’re a very innovative group, receptive to technology,” Factor said. A turnkey system has since been approved for statewide deployment, and 10 states have joined a Colorado-administered pooled fund program to study ATMA use over the next three years. Caltrans is scheduled to deploy a system this summer, and Factor hopes England will approve a national rollout by year’s end.
While Colorado is working with new vehicles, Missouri chose to send two trucks to Florida for retrofitting. “We’ve had several employees who’ve actually been hit twice” driving an attenuator, said Chris Redline, district engineer for Missouri’s MoDOT Northwest region, via a video. One hundred in-state work zone crashes in four years, increasing traffic and distracted/aggressive drivers led Redline to seek an unmanned solution. “It’s a very odd feeling looking into that rear-view mirror, and you see a truck or a car barrelin’ down on you. …It’s real spooky out there.”
Redline put his two-truck retrofit cost at $549,000, with federal funds assisting the upgrade. A pilot program is now operating in Kansas City, with statewide rollout pending legislative approval. “It’s the right thing to do,” Redline said. “The technology is there.”
Continuous improvement based on user feedback is envisioned: more robust communications and GUI; encryption and frequency hopping; added redundancy; optical detection; tuned-up navigation and communications. The goal, per Factor: “To eliminate single-point failure.”
Last June, Kratos representatives testified at a transportation committee of the Pennsylvania Senate, arguing alongside Penn DOT in favor of ATMA deployment. They were joined by a TMA truck accident survivor. The motion passed both houses unanimously and the governor signed it. “This is a technology that is used in a very controlled environment,” Factor noted. “It has all kinds of warnings, signs, lights. For that reason, it’s very acceptable by the general public.
“Everything about Kratos is about improving the envelope for the warfighter,” he concluded. “But the company can pivot, and improve the lives of workers.”